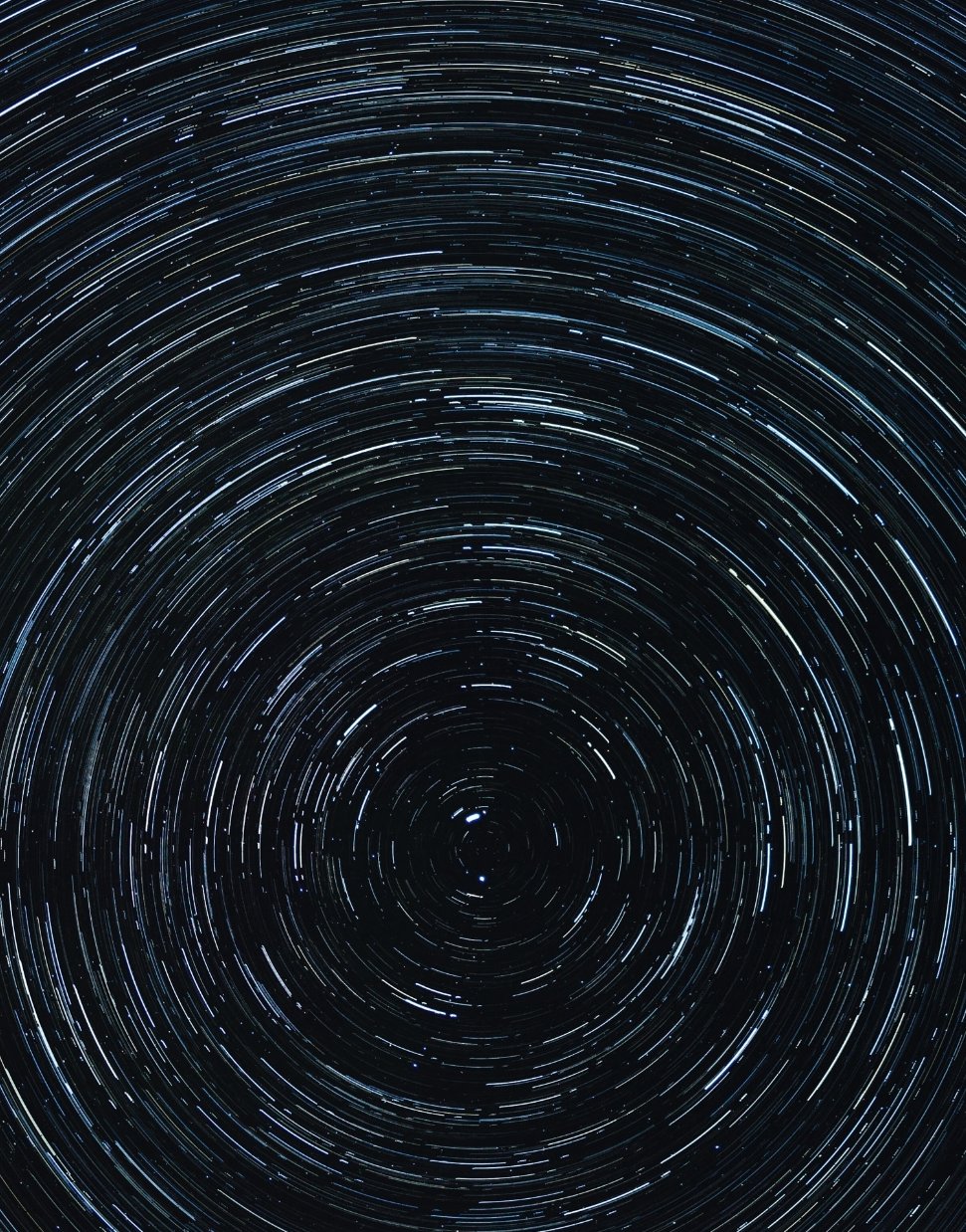
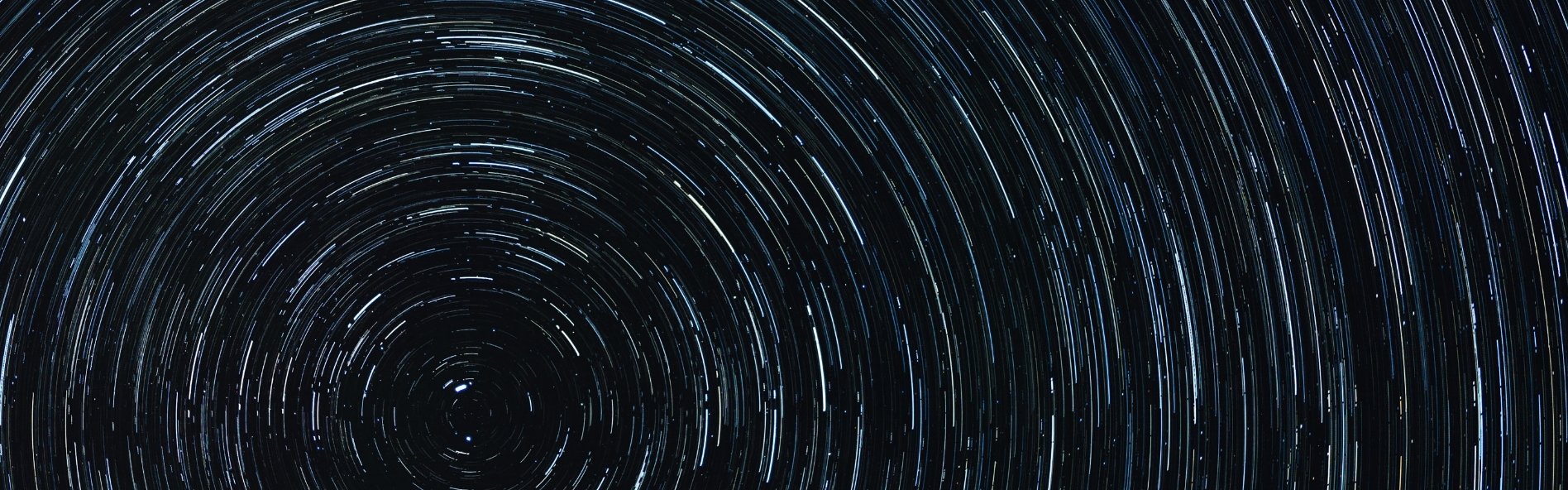
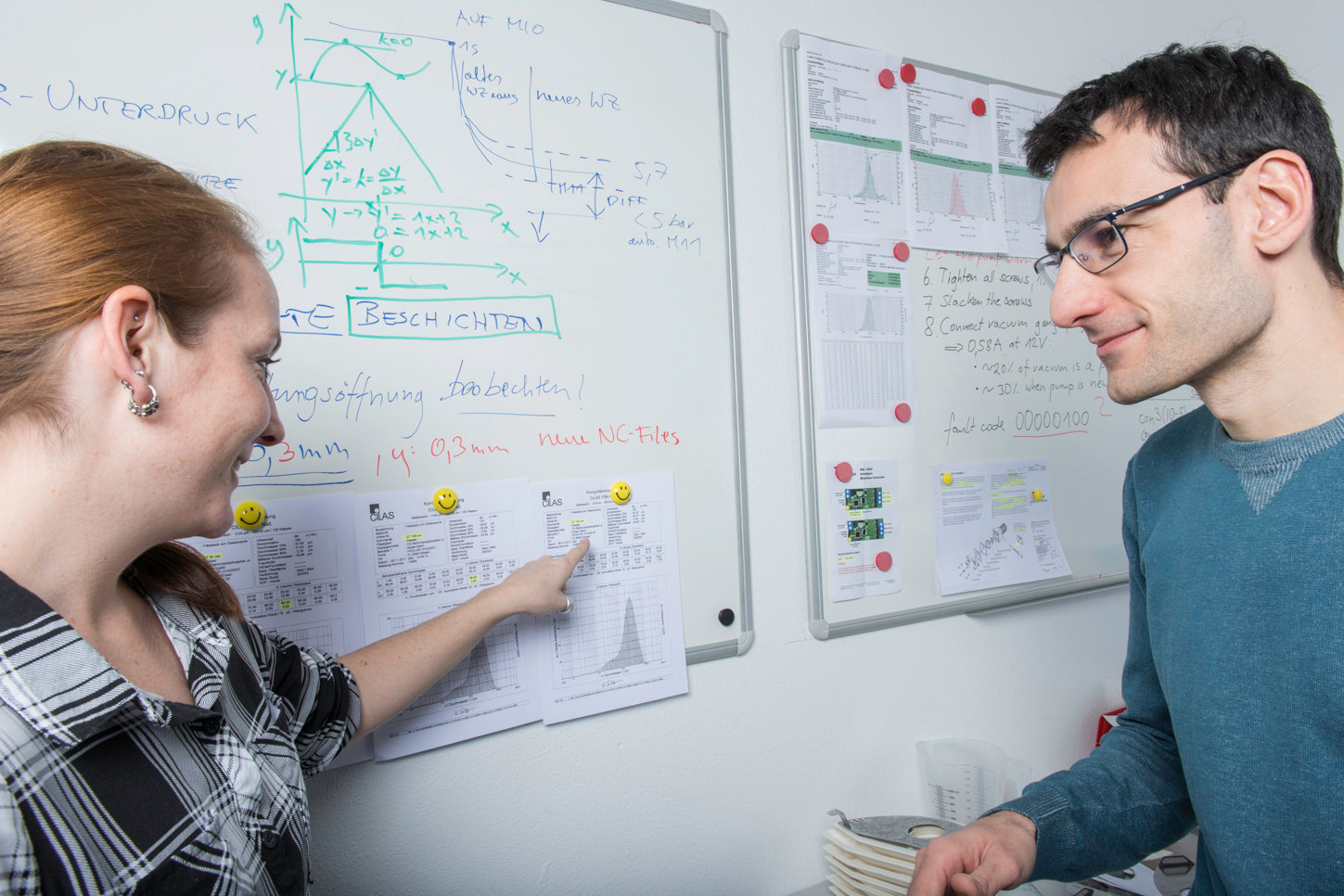
Marktpotentialanalyse
Machen automatisierte Prozesse für euch Sinn?
Wir analysieren euren Markt auf Automatisierungspotentiale – vor allem die Dentalbranche kennen wir wie unsere Westentasche. Entwicklungsaufträge für Industriekunden lieben wir: Bei der Geräte- und Bearbeitungsentwicklung für keramische Materialien achten wir genau darauf, was ihr wirklich braucht.
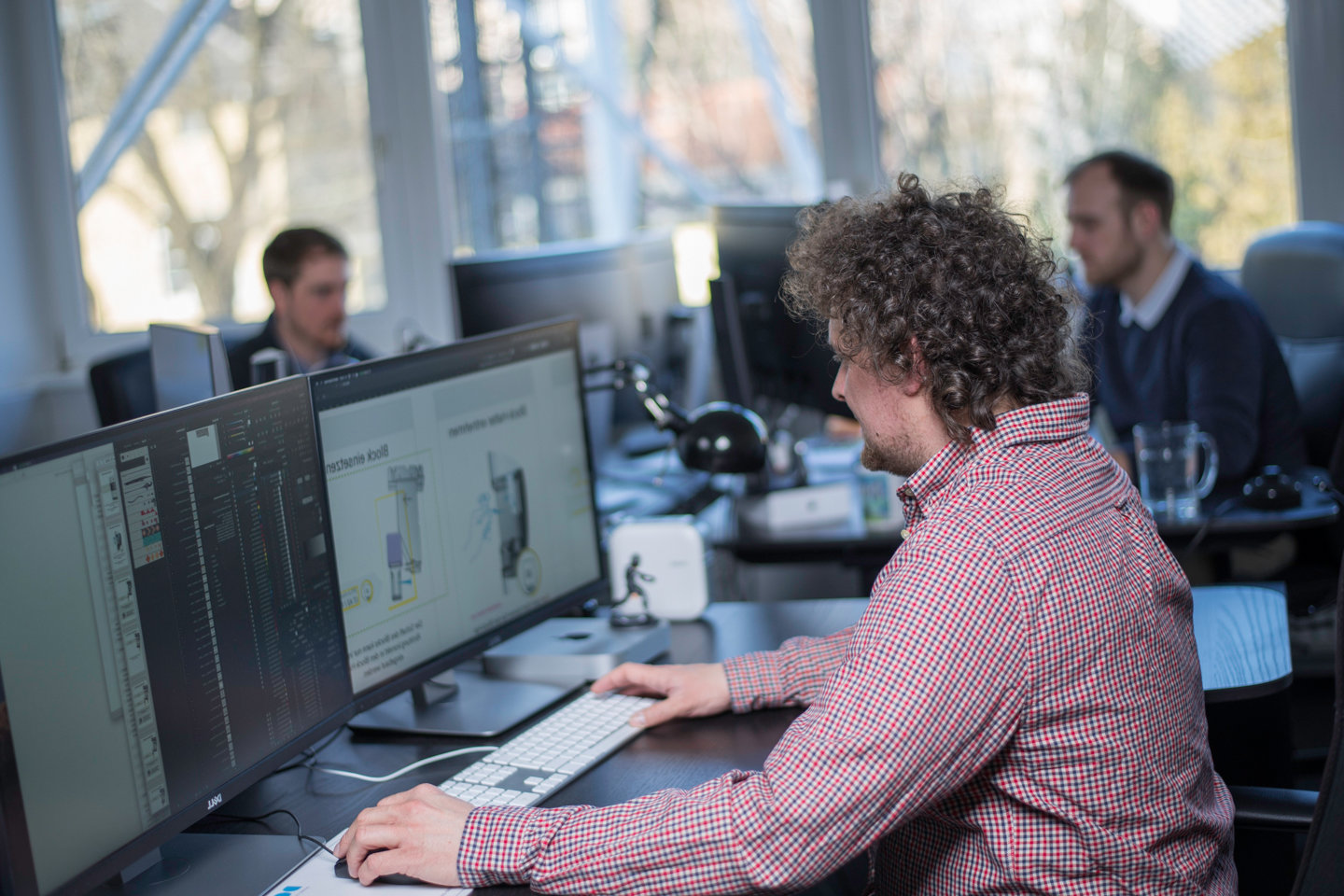
Her mit der Challenge
Lasst uns mal machen: Unsere Kompetenzen
Das bieten wir euch an:
- Firmware- und Softwareentwicklung
- Entwicklung elektronischer Komponenten
- Mechanische Konstruktion mit Schwerpunkt Feinmechanik
- Auslegung und Parametrierung von Antriebslösungen
- Komponenten- und Systemtests
- Verifikation und Validierung
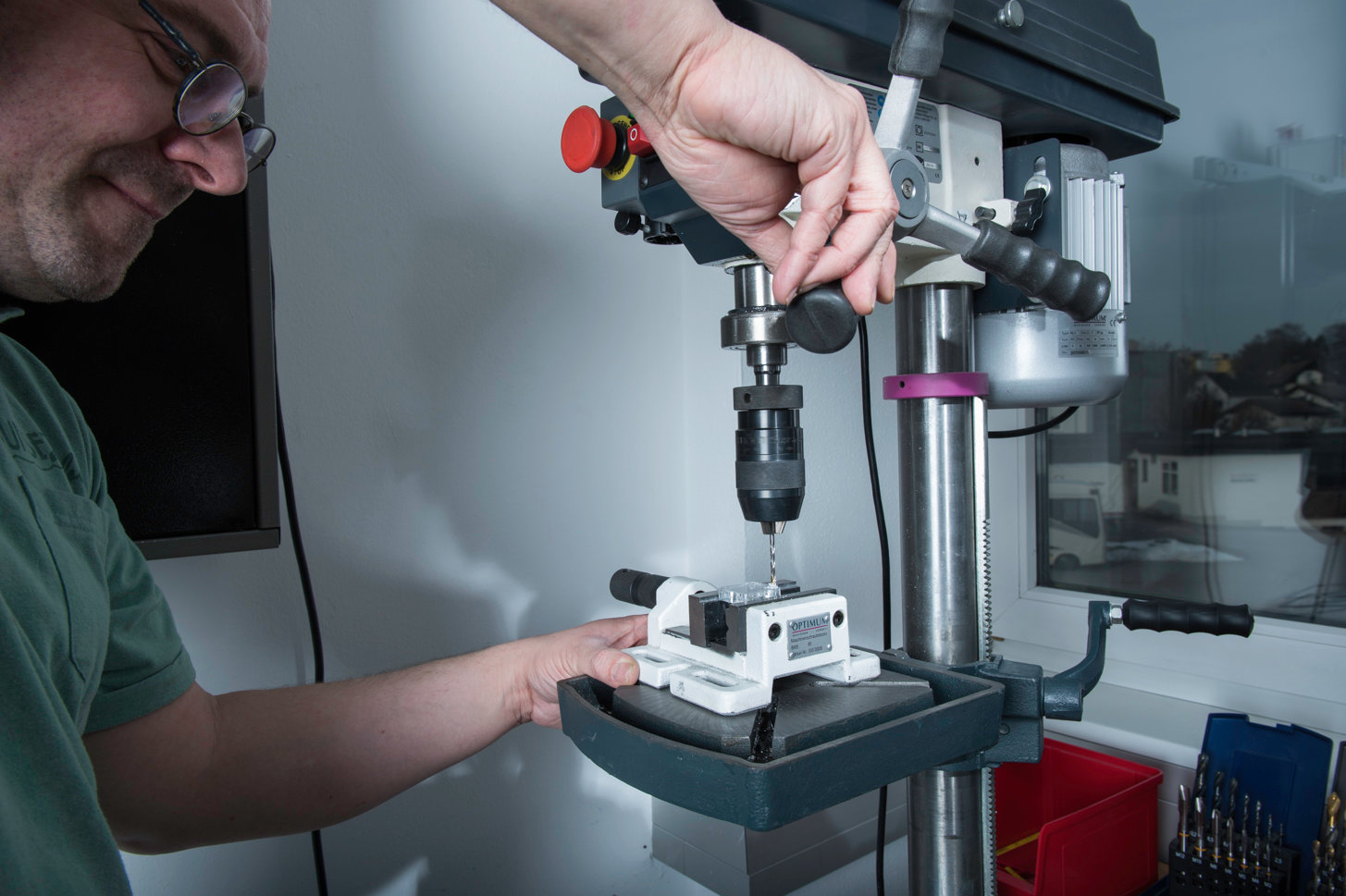
Lehnt euch zurück
Vom Prototyp bis zur Industrialisierung
Einen Prototyp zur Serienreife zu bringen, kann einem den Schlaf rauben. Nicht mit uns! Wir bringen euer Produkt entspannt zur Industrialisierung. Wenn wir dafür einen ganz neuen Produktionsprozess entwickeln müssen, dann machen wir das einfach. Hand in Hand mit euch.